Gas Scenarios
A gas scenario describes the operation of a gas network according to conditions specified in scenario properties and events. A gas scenario determines the distribution of pressures, flow rates, temperature, and composition of gas across the network nodes and branches. The conditions at which these variables are evaluated are specified by the events and profiles of the gas scenario. The properties and settings of a gas scenario define its time span and resolution, as well as the mathematical equations (e.g., equation of state) and numerical tolerances adopted for the solution.
Two types of gas scenarios can be selected in SAInt: a steady state scenario (SteadyGas
) and a dynamic scenario (DynamicGas
).
1. Steady state gas scenario
A steady state gas scenario (SteadyGas
) is used to analyze a snapshot of the operation of a gas network.
It describes a condition for a gas network where the parameters that characterize the gas flow and the network objects are independent of time (i.e., the system is in a state of equilibrium).
The steady state gas network simulation considers gas quality, composition, and temperature tracking. The mathematical model is based on the following equations:
-
pressure drop equations across the from- and to-node of pipelines;
-
nodal continuity equations;
-
control modes, set points, and constraints of compressors, control valves, valves, entry and exit stations, underground gas storages, and LNG Terminals.
The resulting mathematical model is a set of non-linear equations solved using a Newton-Raphson linearization algorithm.
The properties of a SteadyGas
scenario allow specifying solver and time-related information, as well as general attributes and chart visualization options, when accessed using the property editor.
Solver settings provide control over the residual tolerances and the maximum number of iterations admitted during the numerical solution of the steady state fluid-dynamic problem.
Time settings are included in steady state scenarios with a 1-hour time window and time step.
In a SteadyGas
scenario, it is necessary to have at least one pressure and one flow setting in each hydraulic subsystem to search for a solution. In some special cases and in very simple systems, the "control mode change logic" implemented in SAInt may also consider unfeasible combinations where the previous constraint is not satisfied. To avoid such cases SAInt will automatically try to manage the control mode to ensure that at least one pressure or flow setting is always available. The user is advised to check the log of the simulation to verify for any constraint violation or control mode switching.
Table 1 provides an overview of the solver’s properties for a SteadyGas
scenario, while Table 2 shows the time-related properties.
Display name | Description |
---|---|
|
The residual tolerance for linearization steps. The default is 1.0E-5. |
|
The maximum number of iteration steps for linearization. The default is 50 steps. |
|
The maximum number of iteration steps for constraints handling loop. The default is 10 steps. |
|
Select the type of linear solver to use. Choices are: "Pardiso" and "SparseLU". Default is "SparseLU". |
Display name | Description |
---|---|
|
Start time of the scenario. The default is to set the calendar day and hour of when the scenario is created. The property is not relevant to the solution of the simulation. |
|
End time of the scenario. The default is to set the calendar day and one hour plus of when the scenario is created. The property is not relevant to the solution of the simulation. |
|
Total simulation time window. It is set to a fixed one-hour duration. The property is not relevant to the solution of the simulation. |
|
Time step for the scenario. The property is fixed to 60 minutes, and it is not relevant for the solution of the simulation. |
|
The number of time steps for the scenario time window. The property is fixed to 1 time step, and it is not relevant for the solution of the simulation. |
2. Dynamic gas scenario
A dynamic gas scenario (DynamicGas
) scenario analyzes the operation of a gas network under time-varying boundary conditions and network object properties.
A DynamicGas
scenario is characterized by a time window, identified by the start time and the end time, by a time resolution, described by the time step, and by an initial condition, constituting the operational snapshot of the system prior to the beginning of the scenario.
The dynamic gas network simulation considers gas quality, composition, and temperature tracking. The mathematical model is based on the following equations:
-
pressure drop equations across the from- and to-node of pipelines;
-
nodal continuity equations;
-
control modes, set points, and constraints of compressors, control valves, valves, entry and exit stations, underground gas storages, and LNG Terminals.
The resulting mathematical model is a set of nonlinear, implicit finite difference equations solved using a Newton-Raphson linearization algorithm.
In a DynamicGas
scenario, events can occur at any time point within the scenario time window.
The events of a DynamicGas
scenario can be assigned profiles which can change their value over time.
The properties of a DynamicGas
scenario allow specifying solver and time-related information, as well as general attributes and chart visualization options, when accessed using the property editor.
Solver settings provide control over the residual tolerances and the maximum number of iterations admitted during the numerical solution of the steady-state fluid-dynamic problem.
Table 3 provides an overview of the solver’s properties for a DynamicGas
scenario, while Table 4 shows the time-related properties.
Display name | Description |
---|---|
|
The residual tolerance for linearization steps. The default is 1.0E-5. |
|
The maximum number of iteration steps for linearization. The default is 50 steps. |
|
The maximum number of iteration steps for constraints handling loop. The default is 10 steps. |
|
Select the type of linear solver to use. Choices are: "Pardiso" and "SparseLU". Default is "SparseLU". |
Display name | Description |
---|---|
|
Start time of the scenario. The default is to set the calendar day and hour of when the scenario is created. The user can edit this property or can specify its value in the scenario dialog window during the creation of a new scenario. |
|
End time of the scenario. The default is to set the value to plus one calendar day compared to |
|
Total simulation time window. It is derived by considering |
|
Time step for the scenario. The default is set to 15 minutes. The user can edit this property or can specify its value in the scenario dialog window during the creation of a new scenario. |
|
The number of time steps for the scenario time window. The property is calculated by dividing |
|
Name of the scenario whose terminal state is used as the initial state for the current scenario. Default is set to none. This is a required property for |
Figure 1 shows an example of the time settings and their graphical description of a dynamic gas scenario available in the Scenario Dialog.
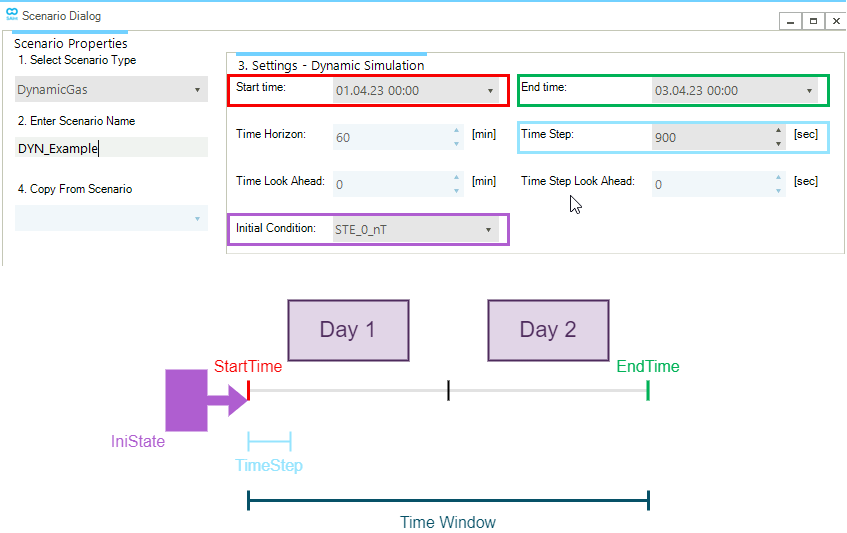
Any (quasi-)dynamic scenario can not last longer than 68 years. SAInt will inform the user of this violation and prevent the scenario from being created. |